Industry 4.0: Enabling Smart Factory with Smart Manufacturing
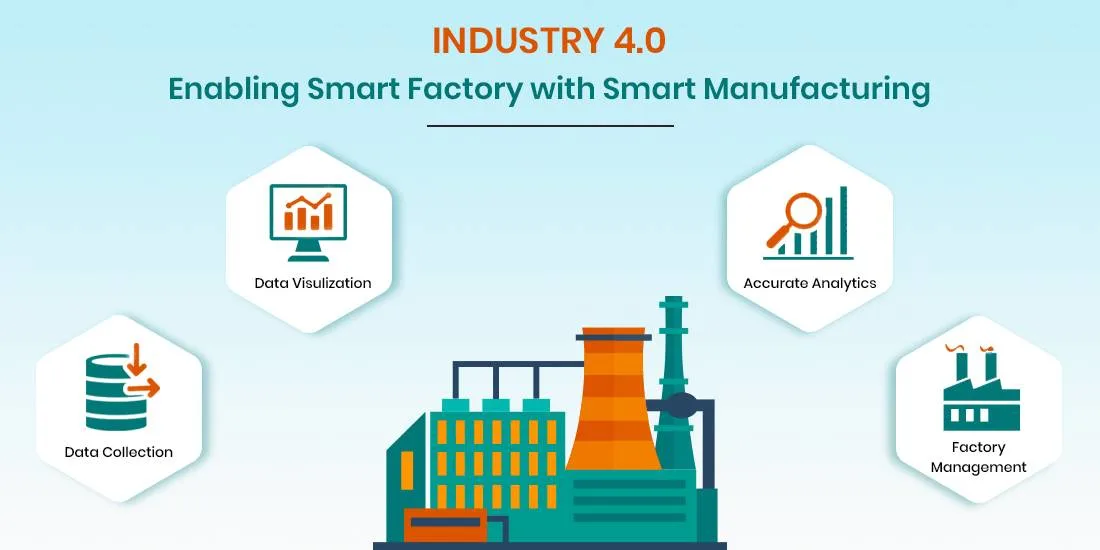
Introduction
The industrial IoT technology has evolved ever since the intelligent algorithm-based automation for manufacturing has gained advancements. From pharmaceutical to automotive, the manufacturing industry has realized the great potential of IoT as the smart factory initiative is now adopted by 67 percent of companies in the industrial manufacturing. The smart factory revolution is built on an IoT-enabled system that connects and unites previously disconnected devices and systems and leverages the data they produce to generate actionable real-time insights.
Also formerly considered as Industry 4.0 technology, IoT solutions help optimize manufacturing processes to enable intelligent automation and smart manufacturing. The smart system of industrial manufacturing is powered by the network of interconnected IoT sensors, devices, factory equipment and automation software combined with data analytics. Apart from managing asset performance and production efficiency, smart factory IoT also helps manage inventory and supply chain and stock replenishment processes.
We will explore the role of IoT as a smart factory technology and how it impacts industrial manufacturing processes.
Smart Factory Revolution
The smart factory system is a future-focused concept of factory automation and is based on advanced intelligence which goes beyond the traditional concept. With the help of IoT technology, Smart factory revolutionizes the way manufacturing processes are handled and executed, transforming the entire set of processes into an intelligent, transparent, scalable interconnected system.
By assembling all the operational and physical assets, equipment and processes with IoT technology, the smart factory becomes capable of smoothly managing the huge volume of the production lines. As IoT also syncs all the system-wide data generated by devices and sensors, manufacturers can resultantly gain efficient control over operations, which results in:
Optimized equipment capacity
Real-time adjustments
Increased production efficiency
Predictive maintenance
Minimum downtime
How IoT helps create a futuristic smart factory
Some of the core components of the manufacturing industry where IoT technology places massive impact are:
Smart and efficient data collection
The most essential aspect of the smart factory 4.0 system is having a smart, efficient data collection and management system that securely fetches and stores crucial data from your ongoing processes, connected devices, and equipment. When perfectly implemented, IoT-powered smart manufacturing process supports myriad connected devices, PCs, ERP systems and cloud applications for flawless, secure data management.
Data visualization and informed business decisions
As the IoT system also provides a clear interface to show operational data, it leads to increased awareness and efficient control over factory processes. Also, as the data across all the local equipment and assets are contextualized on one common IoT platform, it is easy to use the minute, well-interpreted data to make quick and informed business decisions.
Accurate Analytics and Reporting
Implanting the network of IoT sensors, advanced machine learning algorithms, and interconnected equipment, one can easily sync all the data to generate real-time insights. As IoT applications leverage distributed intelligence and historical data to produce powerful predictions and estimates, the final outcome is accurate analytical conclusions and reports.
Mobile-powered factory management
Manufacturers active in a smart factory can keep the real-time watch on continuous processes, locally or remotely, using mobile-enabled IoT solutions. Mobile IoT empowers your workforce with live operations analytics to quickly locate various assets and materials, closely monitor them for quality check and manage overall safety.
The impact of IoT on diverse smart factory components
Smart factory technology powered by IoT devices plays many roles and impacts multiple aspects of smart factory including overall efficiency, quality, and safety. Here is how IoT technology touches the diverse components of smart manufacturing:
Manufacturing operations
As every stage of a smart manufacturing unit is properly optimized with IoT architecture, manufacturers can gain more time to understand the reasons for process inefficiencies and eliminate unwanted redundancies.
Quality assurance
With the help of powerful IoT sensors and connected components of a smart factory, manufacturers view critical data on product defects and accountable production units. Such data along with other collected data on production lines can help detect the source of quality issues.
Predictive factory maintenance
Being a part of smart industry 4.0, smart factory IoT solutions can help identify equipment maintenance or failure in advance before it leads to massive overhaul and unplanned downtime. As manufacturers can capture minute data on equipment performance and health, they can predict and schedule maintenance and minimize downtime and maximize productivity.
Inventory management
IoT interconnected system provides the ability to automate stock replenishment and inventory management by enabling real-time tracking of frequently used materials and items that need restocking. In addition, with the help of real-time tracking of the fleets and end-to-end visibility of goods, manufacturers remain informed of the exact tracking location of items in transit and can predict the arrival of shipments.
Energy-saving and safety
IoT helps gain insight into substantial information such as energy consumption, environmental safety and in-premise caution for possible injuries, creating a more sustainable, energy-efficient and safe process. Machine sensors in IoT help manufacturers monitor and optimize the dissipation of energy and water, leading to environmentally sustainable operations.
Cost-effective Warehouse processes
The smart IoT network helps optimize warehouse process efficiency and minimize labor costs by controlling the movement of inventory stock. The smart factory enables you to easily maintain the consistency in how products should be handled, stored and moved in and out of your warehouse.
Rapid Process improvement
Manufacturers can quickly access all the essential information based on real-time analytics and directly feed desired responses and adjustments to systems and production lines to improve the process quality in the shortest possible time.
Major business areas where IoT-smart factory benefits
With IoT-powered smart factory technology, you are likely to attain the following business advantages:
Maximum productivity
A manufacturing process with optimized asset performance means maximum productivity and consistent output. IoT provides clear insightful data on asset performance and equipment functioning to optimize asset usage, maximize its capacity and minimize asset downtime. As a result, you observe minimal waste, improved operational efficiency, and high-volume production lines.
Superior Product Quality
Enabling reliable data handling capability and display of real-time process analytics, IoT solutions keep you updated on trends and methods to improve product quality. By having the ability to oversee operational data of your smart factory, you can quickly gain access to potential product defects and resolve it to achieve flawless product quality.
Cost-efficient operations
Implementing a smart factory with well-managed data elevates process standards and automates all or some parts of manufacturing operations. With an IoT-connected network ensuring effective data management, uninterrupted operations, reduced maintenance downtime and improved equipment performance, you experience a great chance to enhance the overall cost-efficiency of factory operations.
Unbreakable security
A smart IoT factory is often powered by third-party cloud solutions with high-security standards to ensure secure process automation and control. The IoT provider follows stringent industrial data security guidelines while promising a secure development life-cycle (SDL). This translates to unbreakable smart factory data security and data loss protection standards for your industrial projects such as limited user access, user authorization, and network encryption.
Sustainable operations
Since IoT sensors and algorithms are low-energy automation applications that efficiently optimize the capacity of workplace assets, it fosters a more sustainable environment. Maintaining sustainability and environmental safety is one of the modern industry practices, and the smart factory concept implements them by automating repetitive manufacturing process components.
Project scalability
IoT-enabled smart manufacturing units are simplified, flexible and compatible to fit multiple industries. IoT solutions for smart processes are also designed with an easy-to-integrate architecture that can be scaled whenever you scale your factory size and capability. The intelligent automation in IoT has an extensive lifecycle and supports a wide range of units from single machines to well-synced parallel production lines to the future extensions of your production assets.
Shaping the smart Factory with powerful IoT
As the idea of the smart factory is now becoming reality, we can understand the role of industrial IoT in creating a smart, intelligent and well-managed manufacturing process. The end-to-end manufacturing system built with industry 4.0 technology effectively collects a massive amount of data coming from sensors and devices and uses intelligent algorithms to process and analyze the data patterns. The result eventually is optimized production lines, better supply chain management, rapid stock replenishment, predictive maintenance, and minimum downtime. IoT technology thus helps bring the future of smart factories close to your horizon, offering well-engineered solutions that boost efficiency, productivity and sustainability.